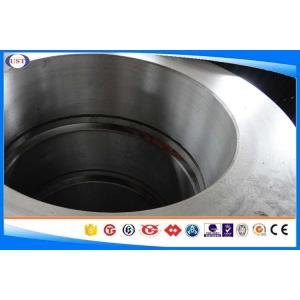
Add to Cart
Professional AISI 1035/S35C Carbon Steel forged steel rings
Applications
The following are the major applications of AISI 1035 carbon steel:
Carbon steels have carbon as the key alloying element in their composition. They also contain up to 0.4% silicon and 1.2% manganese. In addition, the residual elements such as copper, molybdenum, aluminium, chromium and nickel are present in these steels.
AISI 1035 is a water resisting carbon steel whose wear resistance and hardenability are increased by the addition of small quantity of chromium.
The following sections will discuss in detail about AISI 1035 carbon steel.
|
HEAT TREATMENT
Heat treatment is carried out on this grade to render it suitable for machining and to impart to it specified mechanical properties.
Full annealing of small C1035 forgings is carried out between 1550 and 1625 º F (840 – 890 º C) followed by furnace cooling at 50 º F (10 º C) per hour, to 1200 º F (650 º C) and air cooling.
The normalizing temperature range for this grade is typically 1600 – 1650 º F (870 – 900 º C,) Normalizing is followed by cooling in still air. When forgings are normalized before hardening and tempering or other heat treatment, the upper range of the normalizing temperature is used. When normalizing is the final treatment, the lower temperature range is used.
Hardening of this grade is carried out from an austenitizing temperature of 1525 – 1575 º F (830 – 860 º C) and oil or water quenching.
Flame and induction hardening may be carried out by heating quickly to the desired case depth and quenching in water or oil. This should be followed by a tempering treatment at 300 – 400 º F (150 – 200 º C) to reduce stresses in the case without affecting its hardness. A surface hardness of Rc 50 may be obtained by this treatment.
Tempering after normal hardening and oil or water quenching is carried out at 750 – 1260 º F (400 – 680 º C) to give the required mechanical properties as determined by practical experience.
Machinability of C1035 is good providing the full annealing cycle described above is used, ensuring a coarse lamellar pearlite to coarse spheroidite microstructure.
This grade is readily welded with the correct procedure. Welding in the through-hardened or flame or induction-hardened conditions is not recommended.
Low-hydrogen electrodes are recommended together with preheat at 300 – 500 º F (150 – 260 º C.) to be maintained during welding, Cool slowly and stress relieve where possible.