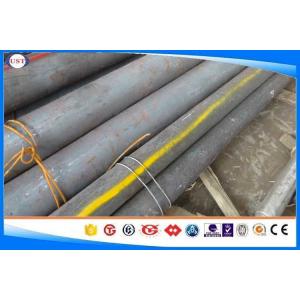
Add to Cart
En26 Hot Forged Steel Bar Round Shape For High Surface Pressures Exist solid round bar
APPLICATIONS:
The steel is suited to applications where high surface pressures exist and friction is to be resisted as in the case of severely loaded gears, axles and pinions.
It is used extensively in most industry sectors for applications requiring higher tensile strength and yield strength than 4140, 4340 or En25 can provide.
RELATED SPECIFICATIONS:
Australia | Germany | Great Britain | BS970 |
AS 14442007 X9940 | W.Nr 1.6745 40NiCrMo10 4 | BS970: Part 3: 1991 826M40 | 1955 EN26 |
Chemical composition%:
Carbon 0.36-0.44
Silicon 0.10-0.40
Manganese 0.45-0.70
Nickel 2.30-2.80
Chromium 0.50-0.80
Molybdenum 0.45-0.66
Phosphorous 0.04 max
Sulphur 0.04 max
Process: EAF+LF+VOD+ Forged+Heat Treatment(optional)
SIZE RANGE:
Round:
Hot Forged: 80mm-1200mm
SURFACE FINISHES:
Black, Peeled K12, Cold Drawn, Turned & Polished H10, H11, Precision Ground H9, H8
Ultrasonic test: According to SEP 1921-84 3Cc
Forging:
Heat to 1150 to 1200°C and hold at temperature until throughly soaked and suitable to forge. Do not forge below 850°C.
Heat Treatment:
To harden EN26 first heat the component to 820 to 850°C and hold at temperature until throughly soaked. Quench the EN26 component in oil, water or polymer as required. EN26 can be flame or induction hardened to achieve a high surface hardness.
Tempering
To temper EN26 heat the component to the required tempering temperature (450 to 660°C), thoroughly soak for 1 hour per 25mm thickness of section, cool in air.
Nitriding
EN26 can be nitrided to give a surface hardness of up to 60HRc. Heat to 500 to 530°C and hold for sufficient time to develop the case depth required, no quenching is required.
Stress Relieving
To stress relieve EN26 heat the component to 640 to 660°C and hold until temperature is uniform through the section. Soak the EN26 component for 1 hour per 25mm thickness of section and cool in air.